INDUSTRY SOFTWARE
Our systems operate both as a functional extension of independent ERP systems as well as fully autonomously.
Solutions offered by CPS Custom Programming Solutions for industry and manufacturing sectors:
Rapid reporting system for errors and failures (Computerized Maintenance Management Systems – CMMS)
A rapid reporting system for errors and failures is a sort of computer assistance for the purpose of maintenance – CMMS (Computerized Maintenance Management Systems). Its principal role is to support the work of maintenance teams in production areas and thus to minimise unexpected downtime (elimination and even prevention of failures), to ensure the continuity of manufacturing processes and to extend the time of the proper functioning of machinery and equipment.
There are two versions of the system available:
Rapid reporting system for errors and failures (CMMS) – standard version
Identification of reported errors
Sonic and light visualisation of errors
To increase efficiency of the process of reporting and removing errors even to a greater extent, the reported errors are visualised by means of light and sonic signals, depending on the their types. On the indicated screens, you can monitor the current state of the manufacturing process, the percentage of accomplished production and its expected schedule. This software version also enables to access the entire record of reported failures.
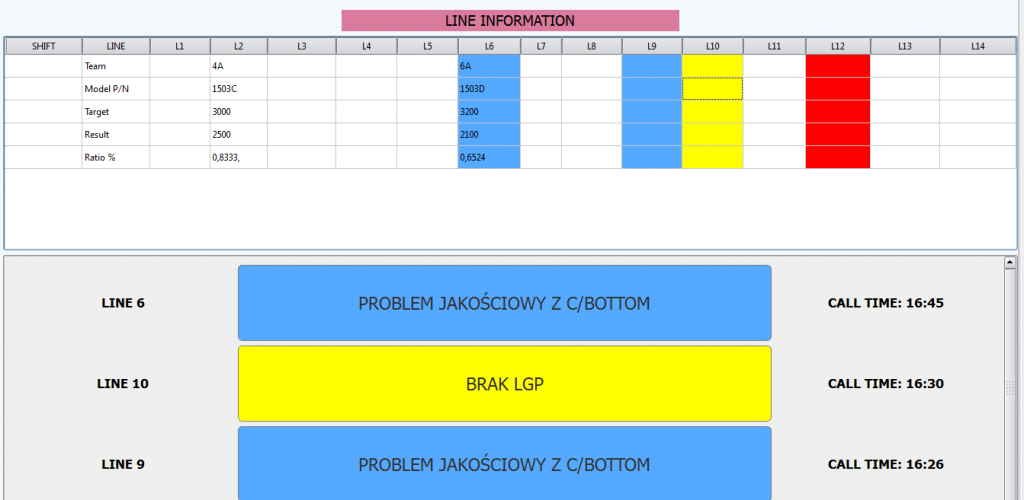
Generating reports
This version of the rapid reporting system for errors and failures also gives the production management full access to the database of detailed reports on recorded failures and errors, the place of their occurrence and personal details of employees who reported them.
Rapid reporting system for errors and failures (CMMS) – extended version
Quick access to electronic documentation or even machine or equipment user’s manual can measurably improve the quality and efficiency of work in production areas. Thanks to complex reports and a knowledge base, which is regularly updated by employees, service technicians and maintenance personnel can easier familiarise themselves with any available information on a given piece of equipment before they proceed to repair activities. Furthermore, they can view the record of reported failures, fixing methods and even access personal details of those employees, who reported the occurrence of the failure during their work shift. Moreover, they can easily find out who fixed it and how long it took to remove the breakdown.
Schedule of planned tasks and selection of appropriate staff.

In the extended version, the database of standard reports can be expanded and modified in accordance with the company’s needs and objectives. Information available in the reports may relate to the most frequent failures, fixing methods, response time etc. Data obtained in such a way will enable a thorough analysis of costs, which will certainly contribute to measurable benefits and prevention of possible failures in the future.
Additional tasks of the rapid reporting system for errors and failures:
![]() |
registry of machinery and equipment |
![]() |
accessories and tools |
![]() |
spare parts warehouse |
![]() |
periodic inspections |
![]() |
log of events |
![]() |
schedules |
![]() |
registry of staff |
![]() |
calculation of costs and the number of man-hours |
![]() |
documentation |
![]() |
resources in a form of attachments |
![]() |
average failure time indicators |
![]() |
mean time between failures (MTBF) indicators |
![]() |
overall equipment effectiveness (OEE) indicators |

Weight checking system
The system has been developed in a way, which enables precise controlling of components in use and pre-packaged on separate production lines. Its purpose is to supervise the assigned production line by using these measurements in practice and generating reports on any possible errors and deviations from a norm.
The system counts the weighted components and decides whether they should be accepted or rejected. Any exceeded threshold values and deviations from a norm are indicated as warnings and alarms. Calculation results are saved on the computer hard drive, which allows for their analysing any time.
Due to the fact that operators are in constant contact with the system, they can easily control a process and its performance on a regular basis. In addition, when we equip a unit with an Ethernet[S2] interface other system users will be able to access database via a company network. The functioning of the weight checking system is based on the independent computer software installed on the computer, to which a weight and a barcode scanner are connected. It is possible to implement any communication protocols into the system, which facilitates integration with weights of various kinds and consequently enables further expansion of the system with another units.
Key features of the system designed for weight checking of products:
![]() |
Real-time scanning of barcodes placed on components |
![]() |
Controlling scanned products in terms of weight |
![]() |
(Light and sonic) alarm signalling in the event of the occurrence of any deviations from adopted norms and limits |
![]() |
Record of elements with their barcodes in database |
![]() |
Local database containing a list of fixed weight products |
![]() |
Possible selection of a type of a product before weighting |
![]() |
Manufacturer’s guarantee |

Consignment note system, integrated with a warehouse management system (WMS)
The integration includes a connection of these two systems in such a way that they can use each other’s resources. Such an integration of systems results in an automatic setting update of the order status into: “Waiting to be processed”, “Sent”, “Waiting in a dock to be received” etc. Any change in status results in applying modifications in all locations connected to the warehouse programme.
While arranging the forwarding of goods, the system makes it possible to draw up and save forwarding documents (import and export) as .xls. The application reduces the time required for the issue of consignment notes and minimises the risk of error in this process. It allows for retrieving shipping addresses from the warehouse database, which eliminates the risk of making mistakes, which could occur when addresses are handwritten by the employees. The application generates successive note numbers on a regular basis, with all pieces of information required for the forwarding of goods.
Basic objectives of the consignment note system, integrated with the warehouse management system:
![]() |
automatic supply management |
![]() |
management of product quantities |
![]() |
visualisation of data (generation of documents as .xls/ xlsx, preparation of consignment notes) |

Visualisation and analysis system for order schedules
Delays in manufacturing and delivery of (sub)components, raw materials or finished products to business partners could result in costly downtime and delays in their production processes and few entrepreneurs can afford this.
It is advisable to implement a system enabling the visualisation of processes being executed such as the visualisation and analysis system for order schedules offered by CPS Custom Programming Solutions in order to optimise the processes carried out at modern enterprises and consequently to avoid the risk of completely running out of manufacturing supply, incapability of keeping up with the work-in-progress as well as to avoid reverse processes, i.e. substantial production surpluses.
The smorystem makes it possible to optimise action regarding the manufacturing plan, which consequently translates into e measurable sales results – a crucial factor for the whole enterprise. The system for visualisation and analysis of order schedules will be connected to the ERP systems of partner companies and will analyse the demand for its own production based on data retrieved from those systems as regards current and planned production within a specified period of time as well as based on the constantly updated order schedule and warehouse stock. This captured data is displayed on screens designated for this purpose, which enables managers to slow down or accelerate the functioning of selected manufacturing lines.
Basic benefits from the implementation of the system for visualisation and analysis of order schedules by CPS Custom Programming Solutions:
![]() |
effective collection of data for the purpose of reverse engineering |
![]() |
analysis of processes being executed at an enterprise, based on the data retrieved from the systems in use at partner companies |
![]() |
visual representation of results |
![]() |
optimisation of processes being executed |
![]() |
reduction of operating costs |
![]() |
elimination of interruptions and downtime |
![]() |
decrease in stock levels and optimisation of the work-in-progress |
![]() |
simplification and acceleration of procedures |
![]() |
adjusting efficiency and working time of both machinery and workers on each line in accordance with the required production schedule |
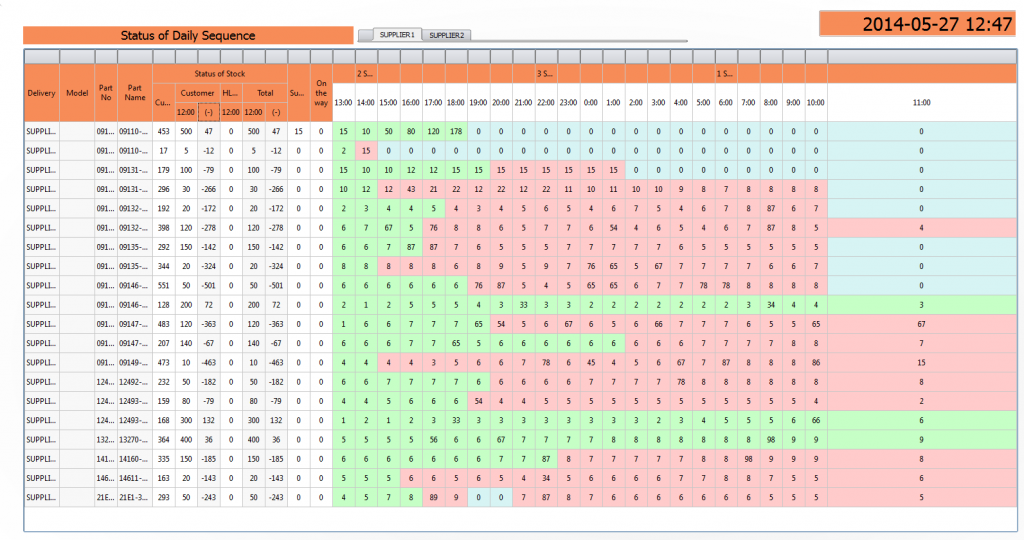